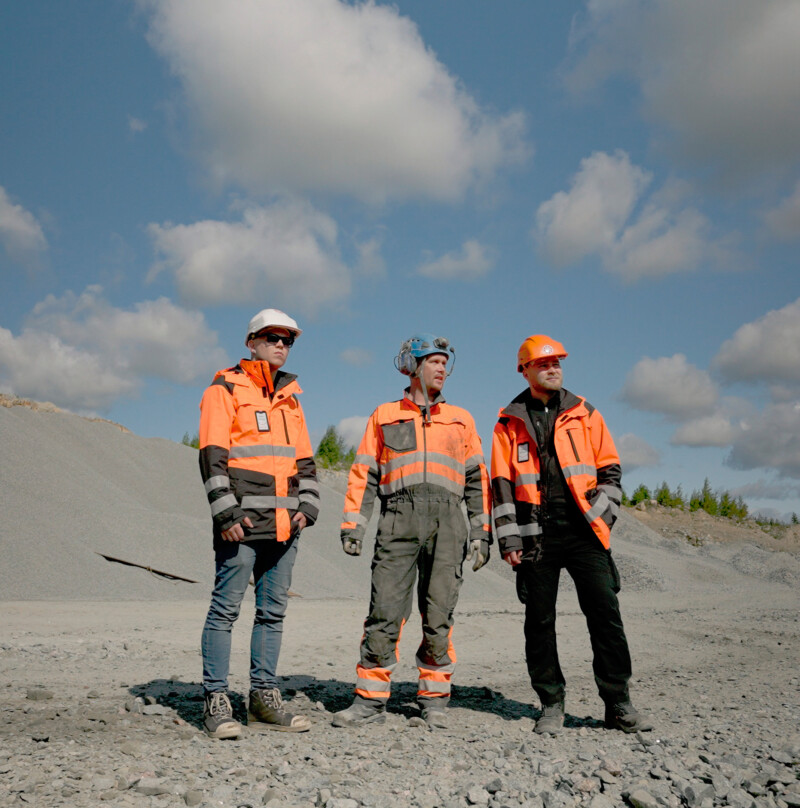
Product support.
We take immense pride in providing more than just manufacturing and supplying parts. Our commitment extends to offering additional technical and engineering support. With a dedicated team, we aim to optimize your equipment’s performance and address any specific challenges you may encounter.
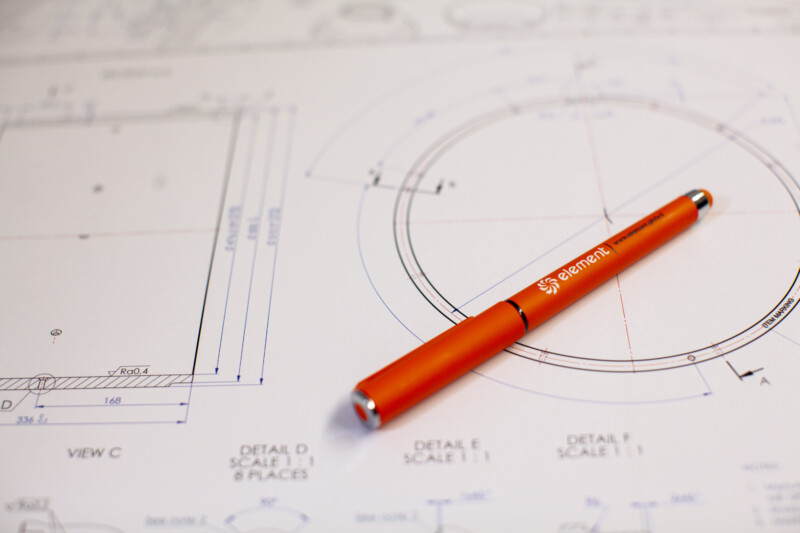
Technical support.
We are committed to providing exceptional technical support to our customers throughout the entire service life of our parts. Whether you have questions, require troubleshooting assistance, or need servicing, our experts are just a call away. With their extensive knowledge and experience, you can rely on our technical support to address any inquiries or issues promptly, ensuring smooth operations and optimal utilization of our parts.
Guide through every step – from selection
of parts to supervising
Our specialists are always on hand to assist you in selecting the perfect wear and spare parts, or their analogs, tailored to your equipment and operational requirements. Moreover, at ELMC, our technical support extends beyond mere assistance as our specialists actively participate in the most critical installation processes, ensuring a seamless and trouble-free installation of our wear and spare parts.
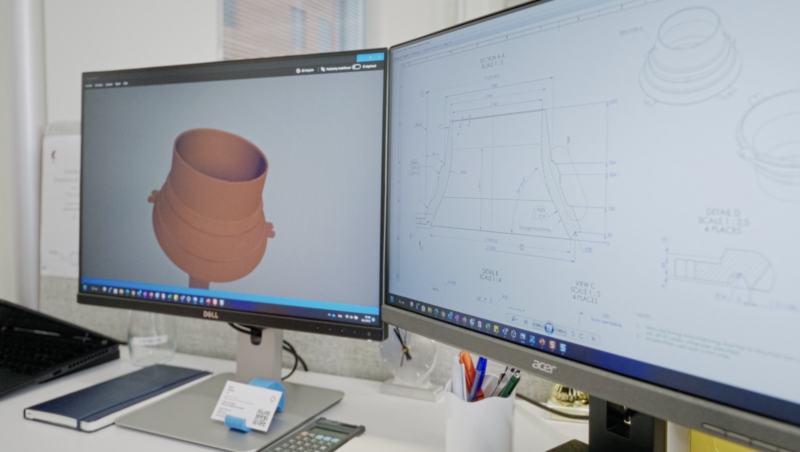
Engineering-to-Order
At ELMC, we understand that each customer’s needs are unique. That’s why our team goes beyond offering analogues of parts from equipment manufacturers. We design and deliver custom-made products tailored to the unique needs and operational challenges of our customers. In situations where your existing part needs upgrading, our experienced team is here to help.
Tailored solution that perfectly aligns with operational objectives
In situations where your existing parts require upgrading, our experienced team stands ready to assist. Through back engineering, we utilize advanced scanning technology to analyze and diagnose areas that may not be functioning optimally. By tailoring geometry or making material modifications, we enhance efficiency, ensuring optimal performance and functionality in your equipment.
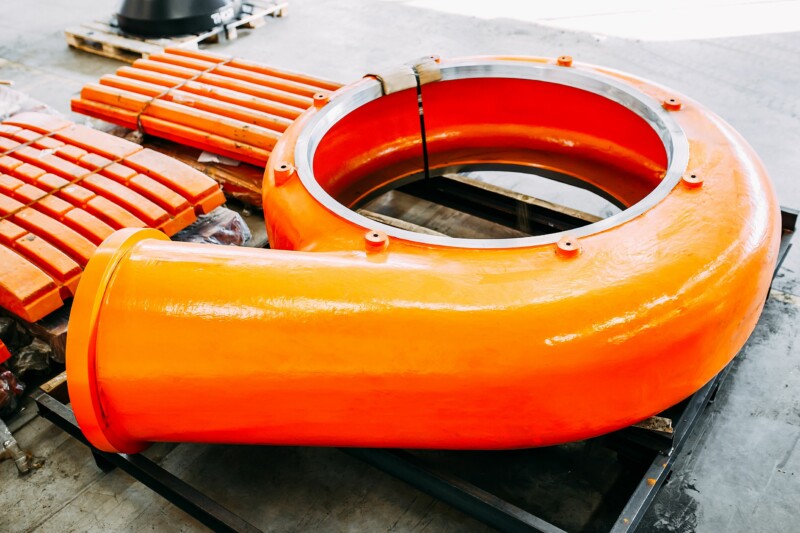
Application support
With a deep understanding of the complexities involved in both slurry handling and crushing processes, our engineers work closely with you to assess your specific requirements and challenges. Through rigorous analysis, we identify areas for improvement and offer tailored solutions to optimize your entire process.
Case studies
Element provides a bespoke project design service in cases where customers require the upgrade of spare part patterns which are currently in operation.
At a gold mining site, the rubber inlet liner of a slurry pump was affected by excessive wear. The company’s specialists replaced it with a HiCr inlet liner. This replacement allowed us to increase the operating time of the spare part and also to improve the repair interval of the equipment.
Element’s specialists designed and developed an impeller with a larger diameter at a gold mining site. This modification was performed on an FLSmidth pump to increase the pump’s capacity via work on the differential head. A similar modification was applied to the Warman 28/24UY-GHPP pump at the iron-ore site. In that case, our engineers designed a thickened inlet liner.
Contact us
Whether you have questions, inquiries, or require support, we are ready to provide the assistance you need. Reach out to us today and let us know how we can help.
"*" indicates required fields