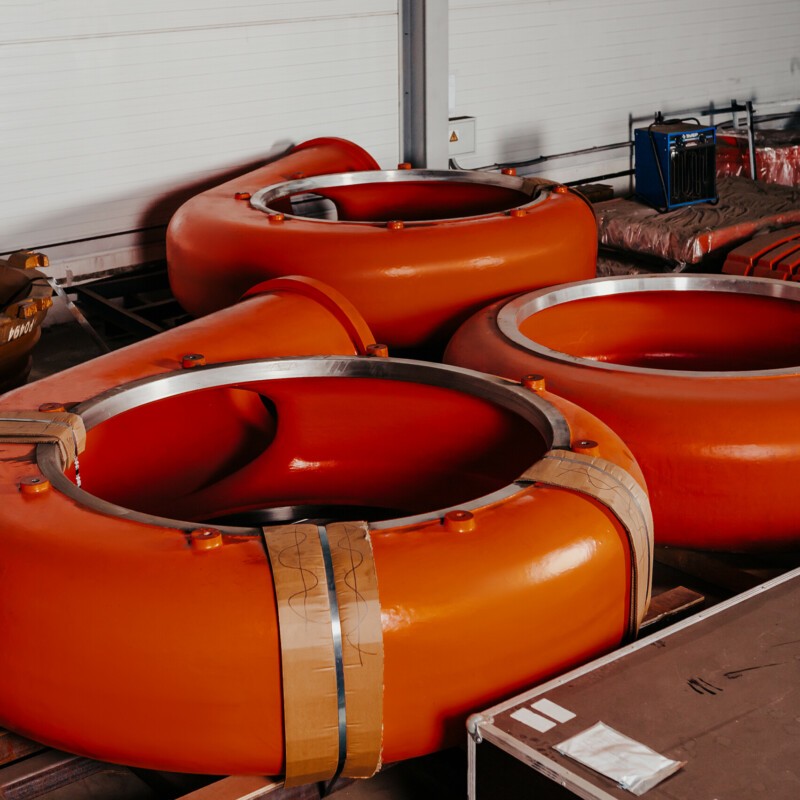
Slurry Pump Parts.
Slurry pump parts are essential for maintaining the continuous operation of a mining plant’s technological chain. While slurry pumps have a simple design, they must meet strict reliability standards since any unplanned shutdown can cause significant process disruptions and financial losses. To prevent downtime and ensure optimal performance, mining plants must invest in high-quality slurry pump spare parts. The cost of maintaining a fleet of slurry pumps represents a substantial portion of operational expenses, making durable and precisely engineered spare and wear parts critical for long-term efficiency and cost control. Just like crusher parts, slurry pump components must be designed for maximum durability to withstand the harsh demands of mining and industrial applications.
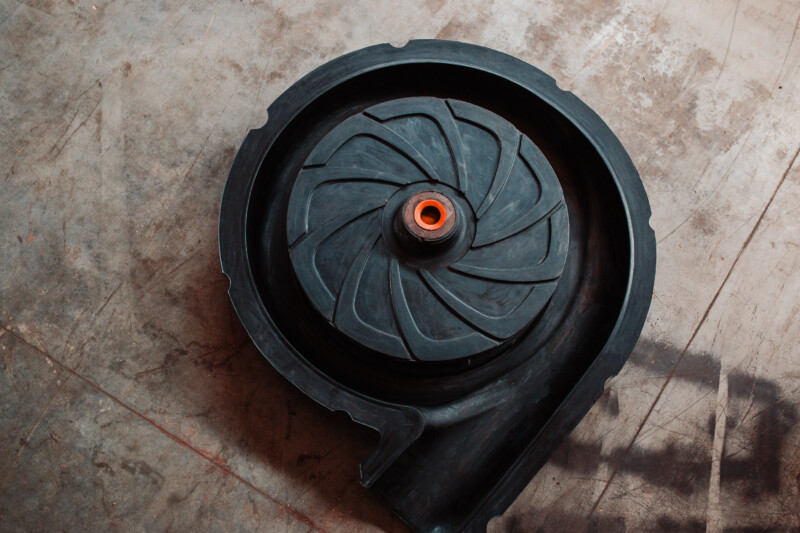
Our range
Each plant is individually engineered, and pumps are selected to match the specific working conditions, ensuring the reliable transfer of the required material volumes between the different processing stages of the plant. Our company offers a wide range of alternative spare and wear parts for slurry pumps, providing proven solutions for all the major brands used at mining plants, including Metso*, Warman*, and Krebs FLS*.
* Element Mining and Construction Oy (ELMC) is not an owner or representative of the brands of the equipment specified on the website. ELMCs spare parts and components are compatible with the specified equipment.
Medium Duty Pumps
Heavy Duty Pumps
Mill Discharge Pumps
High Head Pumps
Gravel Duty Pumps
Tailing Pumps
Vortex Flow Pumps
Froth Duty Pumps
Vertical Pumps
Our parts are compatible with:
Currently, our range includes parts that are compatible with the following machines. Upon request, we can expand our offerings to fit your needs.
Subtype
Model
Materials
Our portfolio includes both the wet-end parts made from various types of high-chrome cast irons and various types of rubber, as well as the full range of necessary spare parts for the maintenance and operation of slurry equipment.
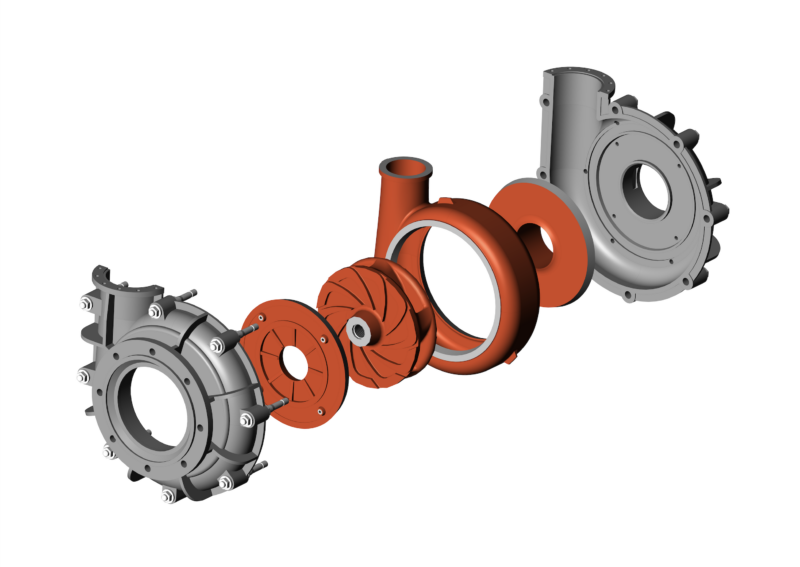
High-chrome White Cast Iron
Parts that come into direct contact with the pulp, such as front and back liners, impellers, case liners, and expellers, are subjected to the most intensive wear. Therefore, we offer parts made of high-chrome white cast iron, perfectly suitable for an abrasive environment.
HIGH-CHROME WHITE CAST IRON GRADE AR27
Standards: ASTM A532 Grade IIIA
Hardness (HBW): >600
Chromium content Cr (%): 27,0
Medium corrosion resistance with high erosion resistance. For operation with pH levels ranging from 5-12.
HIGH-CHROME WHITE CAST IRON GRADE AR30
Standards: N/A
Hardness (HBW): >650
Chromium content Cr (%): 30,0
Perfect erosion resistance for slurry with small and middle particles. For operation with PH levels 3-14. Mostly used in tailing applications or as an option to extend the lifetime of wet-end parts.
HIGH-CHROME WHITE CAST IRON GRADE AR28
Standards: ASTM A532 Grade IIIA
Hardness (HBW): >430
Chromium content Cr (%): 28,0
Adapted for use with acids and in corrosive environments. For operation with pH levels rangin from 3-14. Preferable for slurry wit sulfuric acid, nitric acid or sodiuhydroxide contents.
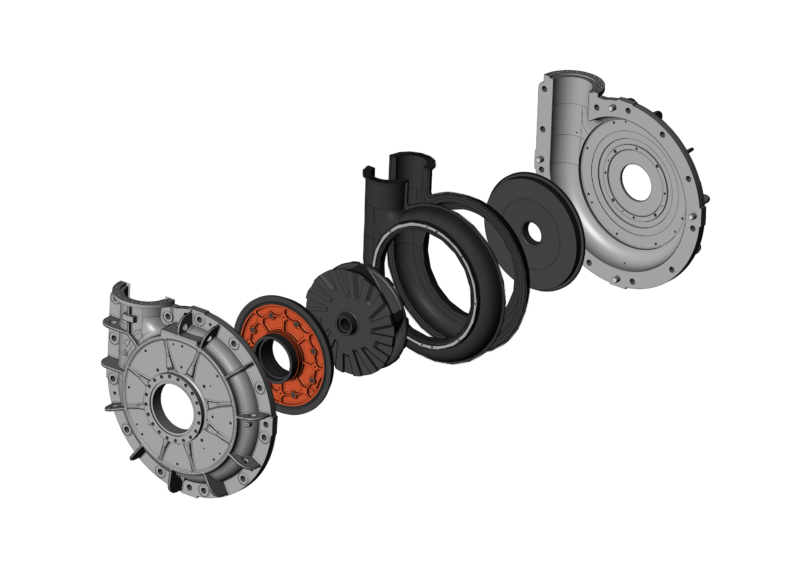
Synthetic Rubber
Synthetic rubber offers a unique set of advantages that make it an excellent choice for certain applications. In some cases, our experts may recommend the use of synthetic rubber over cast iron to enhance durability, reduce maintenance costs, and improve overall system performance.
High Strength rubber based on natural rubber er40/er50
Standards: ME QP-09
Density (g/cmÑ): 1,05±0,05
Hardness (Shore A): 40±5; 50±5
Max. operating temperature (°C): 70
High wear resistance and medium chemical resistance.
High Strength rubber based on neoprene cr50/cr60
Standards: ME QP-09
Density (g/cmÑ): 1,35±0,05
Hardness (Shore A): 50±5; 60±5
Max. operating temperature (°C): 100
High wear resistance and high chemical resistance to trioxygen and oils.
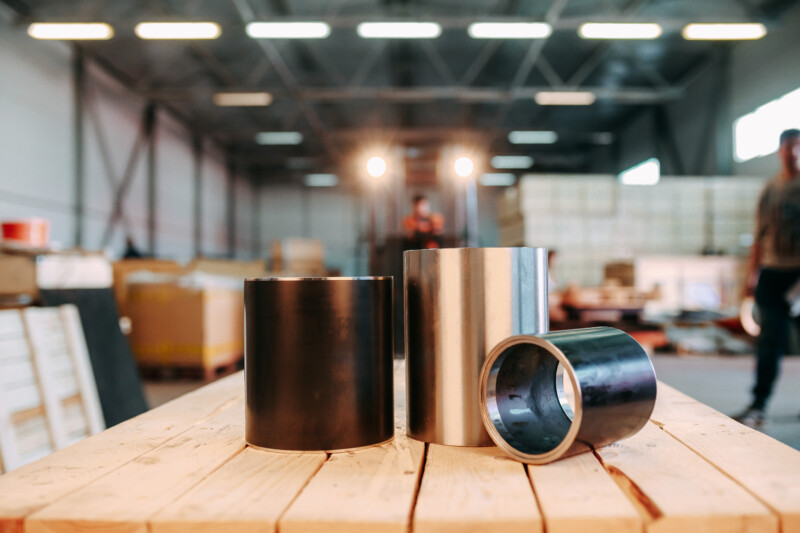
Spare parts
In addition, we provide a comprehensive range of essential spare parts to ensure the smooth operation of your pumps. This comprehensive inventory includes parts such as the gland follower, packing, lantern restrictor, shaft sleeve, and stuffing box. We offer a variety of material options for these parts, from stainless steel for shaft sleeves to bronze lantern restrictors and ribbon PTFE for gland packing.
Case studies
Element provides a bespoke project design service in cases where customers require the upgrade of spare part patterns which are currently in operation. To request an individual project, please download and fill in our question list.
One of the challenges that our customers came to us with was the rapid wear of wet-end parts. A large gold-processing plant assigned us the task of increasing the operating time of the liners for their 10/8 slurry pump. Element’s specialists visited the customer’s site, examined the operating conditions, and determined that the liners’ short operating time was due to an incorrect choice of wet-end part material. Based on the collected data from the pump installation and slurry data, Element’s engineers proposed replacing the metal wet-end parts with natural rubber. This resulted in a 1.5-fold increase in operating time and a decrease of over 2 times in spare parts expenses for the processing plant.
Element supplied a set of wet-end parts to a large gold mining company in March of 2021. Due to the high load of solids, as well as the very coarse and large size of ore after the primary mill, the equipment in the process plant experienced a significant wear rate at the mill discharge circuit. The average operating time of the OEM’s wet-end parts was 1,100 hours and they complied with all of the customer’s requirements. However, replacing these parts entailed high costs. Element provided wet-end parts made from High Chrome White Iron in accordance with their material standard. As a result, the first set of parts lasted for 1200 hours of operation, and the second and third sets demonstrated the same lifespan. Consequently, the customer was able to achieve the same amount of operation time as with OEM parts while incurring significantly lower maintenance costs.
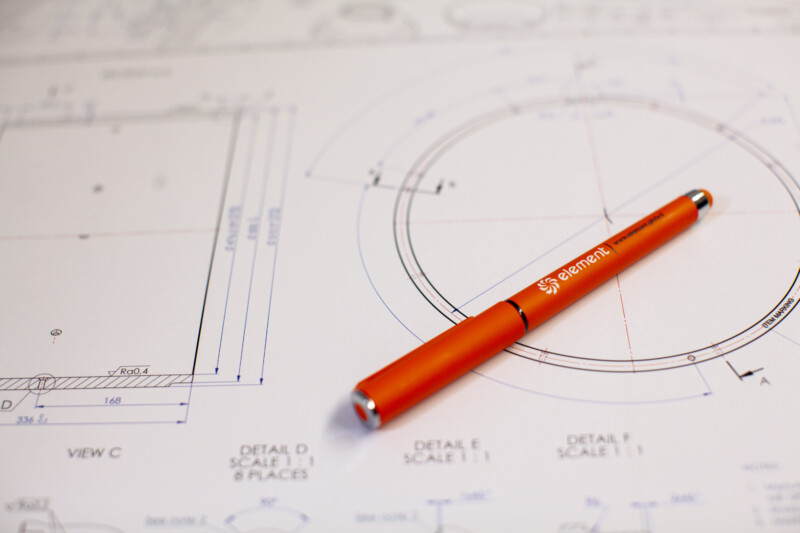
Product support.
In addition to supplying spare parts, our company also gladly takes on complex cases and tailor-made developments as per customer requirements. We thoroughly study the technical and technological parameters of equipment operation, analyze wear of wet-end parts, and can offer optimized solutions to meet customer requirements
Contact us
Whether you have questions, inquiries, or require support, we are ready to provide the assistance you need. Reach out to us today and let us know how we can help.
"*" indicates required fields